Abatement of harmful substances in flue gases
One of the most interesting and innovative projects undertaken by Poppi Clementino’s R&D department recently involves the development of a system for the abatement of harmful substances present in the flue gases emitted during the ceramic production process.

As part of its efforts to investigate new aspects of energy recovery, Poppi Clementino has expanded its R&D division, which now comprises a team of young professionals and an R&D Director working on the development and testing of new technologies.
One of the most interesting and innovative projects undertaken by the R&D department recently involves the development of a system for the abatement of harmful substances present in the flue gases emitted during the ceramic production process. This patented solution involves reusing kiln flue gases in the production cycle, thereby eliminating pollutants while at the same time achieving significant energy savings.
The first applications in the ceramic industry may be adopted over the next few months.
The flue gases produced in the firing process typically contain various pollutants deriving from the combustion of organic substances, such as ash, CO and VOCs, including aldehydes. The aldehydes produced by the thermal degradation of organic substances include unpleasant odorous compounds and formaldehyde, which poses a health hazard. Other pollutants typical of this specific production process include chlorides, fluorides and sulphur oxides (SOx). Clearly, the release of these substances into the environment affects air quality and may be unpleasant or harmful to humans, and should therefore be avoided.
Although a number of flue gas abatement techniques exist, some of them are inefficient or extremely expensive due to their high energy consumption. Examples include thermal post-combustion and cryogenic abatement of volatile organic compounds, although both solutions are excessively costly and do not allow for proper abatement of all harmful substances present in the flue gases.
The advantage of the technology developed by Poppi is that it is capable of reducing VOCs in flue gases while using the heat from the fluid downstream of the afterburner in the spray dryer, a solution that brings significant energy savings.
The VOC concentration after the thermal oxidation process carried out by the afterburner can be reduced considerably to a value of approximately 5.0 mg/Nm3.
As the afterburner operates at a temperature close to 850°C, it completely oxidises almost all the organic substances present in the flue gases, including aldehydes, with levels of abatement of up to about 75% of the concentration of aldehydes normally present in the emissions of a ceramic kiln downstream of the filter.
Operation of the plant
As shown in the figure, the system designed by Poppi involves drawing in flue gases from the ceramic plant through an intake duct (1), followed by filtration by means of a bag filter (2) using sodium bicarbonate as the reagent. This is followed by thermal oxidation by means of the afterburner (3) and subsequent reuse of the filtered and heated flue gases in the spray dryer (5). The latter process allows for additional abatement of harmful substances in the flue gases by means of additional downstream filtration (10).
This treatment sequence ensures significant abatement of polluting by-products (inorganic and organic compounds) without increasing the operating or energy costs and actually achieving savings and greater thermal efficiency compared to traditional methods.
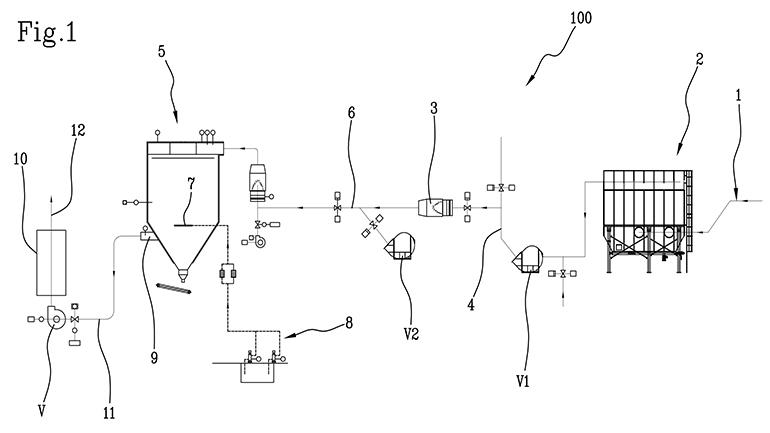
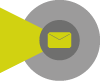
Did you find this article useful?
Join the CWW community to receive the most important news from the global ceramic industry every two weeks