Johnson Matthey
It allows companies in the ceramic sector to test new products and production process innovations without taking up space on their production lines. .

This ambitious project has required continuous cooperation with the most important technology manufacturers in order to create a constantly evolving research centre where all production process innovations can be tried and tested.
A team of specialist technicians is able to assist customers during all stages of new project development and to train their technicians in the technologically most innovative procedures. Superlab is a facility that is able to provide design, chemicals, punches and industrialised products. Customers are given a production formula along with a detailed analysis of production costs per square metre. This guarantees perfect and immediate reproducibility of products on customers' production lines.

In short, Superlab provides dependable solutions (unlike conventional colour and glaze producers who are able to offer ideas but cannot guarantee perfect reproducibility on ceramic tiles). This allows companies to significantly reduce research times and costs. Furthermore, they can consult a team of experts for advice on the most suitable procedures for any type of production (porcelain tile, single firing, high porosity single firing, fast double firing and third fire decoration) and verify the potential of the new applied technologies (double pressing or double filling systems and new methods for glazing and wet and dry decoration).

Superlab technical equipment:
- glaze and body grinding mills (200 kg, 100 kg and 50 kg dry capacity);
- Twin press (Sacmi): one press equipped with decor-pressing systems: Color Dry Press (Tecno Italia) and Spot Feeder (L.B.);
- 4 Rotocolor Large (System);
- 4 Color Dry Line acetate rollers (Tecno Italia);
- 1 D.M.S. micronised granule device for dry applications (Sacmi);
- 1 press for final pressing (Sacmi);
- Dryer (Imas);
- glazing line complete with:
- Double Disc and spray gun (Cimes);
- Brushing machine (IRI);
- Double disc, bell applicator (Cimes)
- Curtain coating system complete with injection systems (Ingegneria Ceramica);
- Aqua wetting system (Ingegneria Ceramica);
- 5-head Rotocolor (System);
- 4-head Laser-Roll (Tecno Italia);
- Double disc (Cimes).
- Modula vertical warehouse (System);
- Screen printing ink preparation system with standardised bases and colours (Assoprint).
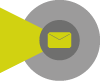
Did you find this article useful?
Join the CWW community to receive the most important news from the global ceramic industry every two weeks
Recent articles
Florim opens a new Flagship Store in Los Angeles
Jun 13, 2025