A biomimetic approach behind the Tenagreen design process
The new Tenagreen binders enable manufacturers to produce thinner slabs, reduce natural gas consumption for firing and adopt a mix of lower grade or recycled clays.

Tenagreen is the end result of a collaborative analysis and design process conducted in cooperation with leading ceramic and porcelain tile and slab manufacturers. The most sought-after innovation regards solutions capable of reducing the thickness and weight of products and consequently lowering emissions, especially in the production of large size ceramic and composite tiles. The sustainability of the production process and of all steps in the supply chain has emerged as a critical factor for competitiveness.
In 2022, this process had to be dramatically accelerated following the outbreak of the Russia-Ukraine war, which initially disrupted and eventually cut off the main supply line for high-grade clays. This disruption led the ceramic industry to urgently seek alternatives to high-grade clays, including the use of locally sourced materials with inferior plastic qualities. This need for alternatives aligned with the pre-existing demand for lighter products using less material, thereby reducing both direct and indirect emissions. It also underscored the importance of enhancing the quality and workability of a diverse range of clays and other raw materials.
The design process for potential solutions had to consider new elements and issues. Lamberti, with its multiple R&D laboratories, extensive experience with materials, and a broad spectrum of disciplinary expertise, was able to guide the design process towards biomimetic approaches through continuous exchanges and transfers of technology and knowledge. The solution, it turned out, was already present in nature.
Trees bend in the wind but rarely break. This resilience is due to their fibres, which are strong yet flexible, and are immersed in natural compounds such as hemicellulose that provide an optimal level of deformability and elasticity.
Like tree fibres, Tenagreen (made from synthetic/natural graft copolymers) integrate with the molecular composition of clays, lending ceramic slabs elasticity prior to firing and integrating with the ceramic microstructure of the slabs, thereby increasing their flexibility and breaking strength. This enables manufacturers to produce thinner slabs, reduce natural gas consumption for firing, adopt a mix of lower grade or recycled clays and produce semi-transparent vitreous ceramic slabs.
Lamberti considers this biomimetic approach to be the new frontier of product design. By studying and imitating nature’s complex yet perfect solutions, it is possible to develop products that respect the natural equilibrium of the planet and offer unparalleled levels of performance. This approach translates natural phenomena into parameters that can be used to explain and understand them. By learning from nature, ceramic technology has developed molecules that enhance the flexibility of ceramic surfaces. In addition, products inspired by the perfection of nature are able to meet the needs of the entire ceramic production process while focusing on sustainability for materials, people and the planet.
Founded in 1911, Lamberti is a speciality chemicals manufacturer with a global footprint, including technology and production facilities around the world. The ceramic division, created in the 1980s in the ceramic districts of Sassuolo and Castellón, collaborates closely with customers, suppliers and equipment manufacturers. The company constantly expands its expertise through partnerships with international scientific laboratories and research centres. It recently expanded its presence in the United States with the purchase of a new warehouse in Lebanon, Tennessee to support its logistics hub in Houston.
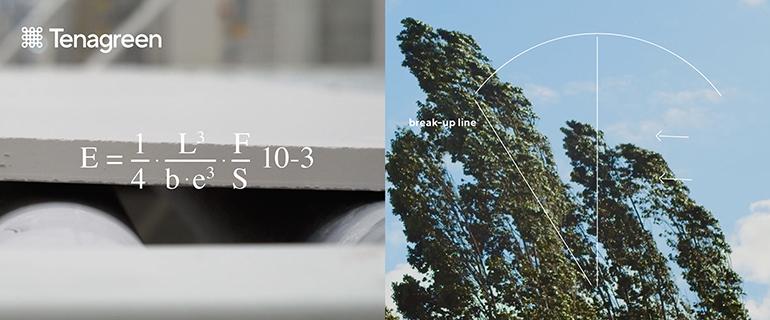
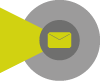
Did you find this article useful?
Join the CWW community to receive the most important news from the global ceramic industry every two weeks