Bongioanni Macchine: mould support plates for energy saving
High performance, energy savings during the drying and elimination of clay wastage are the plus of the solutions.

To comply with current environmental regulations, companies operating in the international marketplace must redouble their efforts to develop innovative and sustainable solutions for maximum energy and raw material savings.
In the 1990s, Bongioanni Macchine designed a mould wear recovery plate which could be mounted on presses in place of traditional solutions to avoid producing tiles with different thicknesses and to save energy during the drying process.
Over the years, the company’s dynamic R&D team improved the solution by adding innovative technical features to meet growing customer demand for higher performance and energy efficiency.
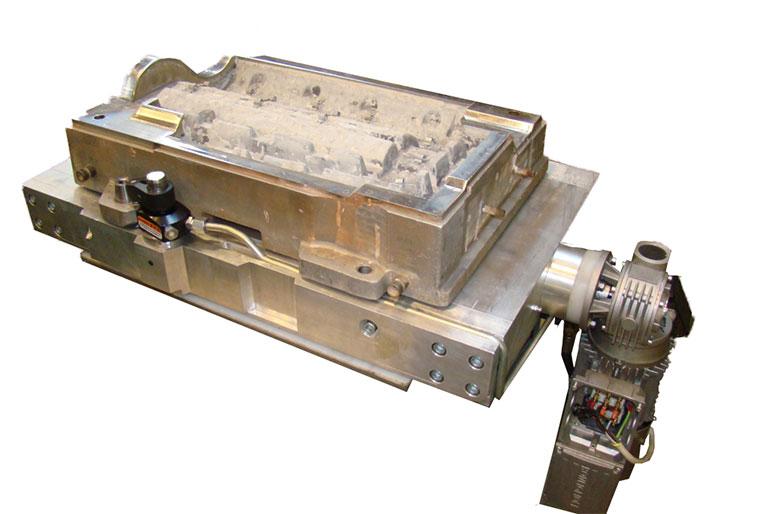
Introduction
Generally, the ratio between the number of upper moulds and the number of lower moulds on presses is 1:6. The upper moulds are replaced in parallel with the lower moulds on the drum face of each press. The operation is repeated every two upper mould changes (in other words 4 hours after the previous face) and the complete drum is renewed over 24 hours.
While this reduces the number of lower moulds, it may give rise to a considerable difference in weight between the tiles, for example between those produced with the newly replaced moulds of face no. 1 and those produced with the moulds of face no. 6 after 20 hours of operation.
An alternative approach that may resolve this issue is to perform a single daily stop, during which all the bottom moulds of the drum are replaced. This allows for more linear control of the weight/thickness of products by fully exploiting the characteristics of the micrometric upper mould support plates designed by Bongioanni Macchine.
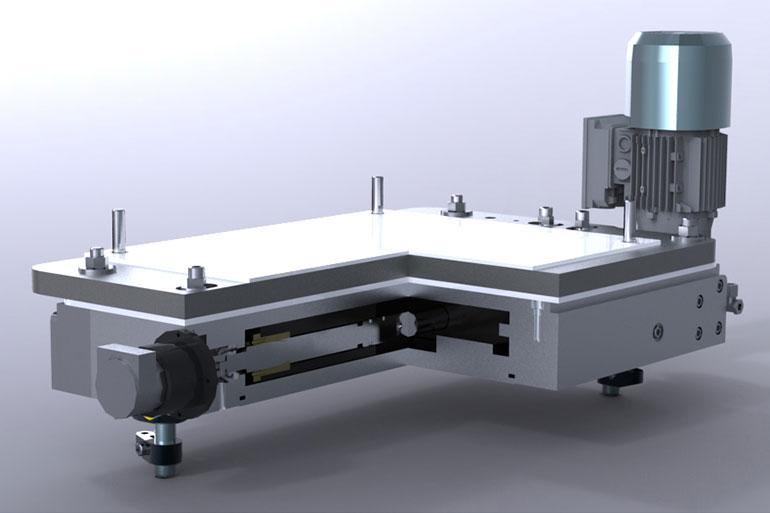
Performing the process and results
The micrometric upper mould support plates are equipped with a robust wedge system driven by an SEW gearmotor that in turn operates a high-precision worm gear system.
On the opposite side to the gearmotor, an absolute encoder ensures micrometric precision of movement and allows the vertical position of the upper mould to be controlled to within a tenth of a millimetre.
Height adjustments can be made by the press operator from the press operating panel either manually or in automatic mode by setting the desired correction (expressed in tenths of a millimetre). This correction is then performed by the software after a number of strokes that can be set from the operating panel.
This makes it possible to reduce the weight difference between products from the normally acceptable value of ±100-150 g (corresponding to a maximum difference between tiles of 200-300 g) to ±50-60 g (100-120 g max. difference).
These results can be achieved through a twofold approach in which the weight of products is checked constantly by the press operators and special attention is devoted to the process of lower mould casting (condition of the master moulds and their coupling frames, state of wear of the border strips, etc.).
According to the statistics, presses perform around 18,000 strokes every 24 hours, so each lower mould completes around 3,120 strokes during its 20-hour lifetime.
The use of a larger number of lower moulds will not affect the daily output of the plaster casting department and consequently plaster consumption because the number of lower moulds required remains unchanged.
The shorter drying time results in considerable energy savings during the drying process (the tiles will all have the same thickness) and eliminates clay wastage.
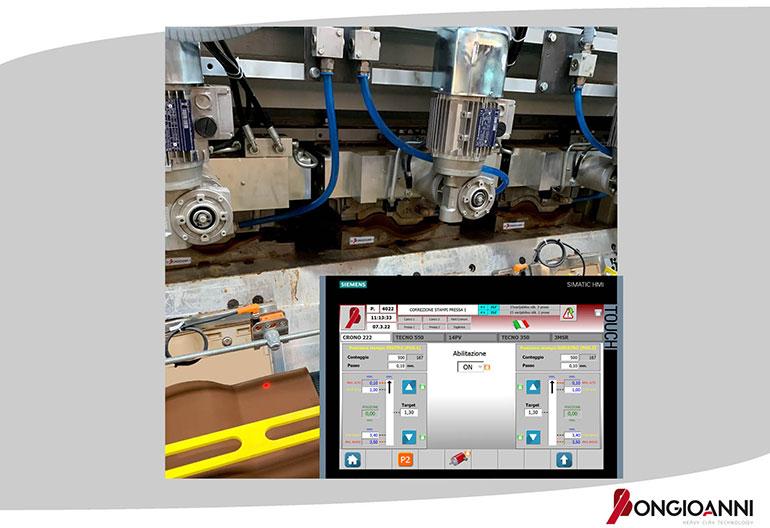
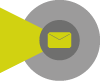
Did you find this article useful?
Join the CWW community to receive the most important news from the global ceramic industry every two weeks