New ventilating cone for sanitaryware drying
Marcheluzzo has developed a new high-efficiency, low-consumption Stand-alone Ventilating Cone, a high-performance solution that applies the same principles and technology as those adopted in the heavy clay sector
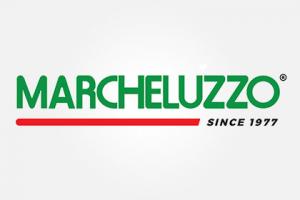
Marcheluzzo has long been promoting perforated plate technology for sanitaryware drying as it allows for a low but uniform air velocity, thereby guaranteeing a correct cycle with all product types even after demoulding.
However, the production of increasingly complex articles has prompted many companies to adopt dedicated pre-drying plants, which means that the pieces undergo further operations (removal of polyurethane supports or manual operations) before arriving at the dryer.
In these cases, the fact that shrinkage has been completed means that the perforated plate solution is not the most advantageous as the air velocity is the crucial factor in the second part of the drying process. Based on these considerations, Marcheluzzo has developed a new high-efficiency, low-consumption ventilating cone, a high-performance solution that applies the same principles and technology as those adopted in the heavy clay sector, the Vicenza-based company’s core business.
All-in-one flexibility, efficiency and energy savings

Successfully presented at Tecna 2022 in Rimini, the new model is called the Stand-alone Ventilating cone due to the fact that it is detached from the dryer structure and can therefore be placed anywhere within the cells and repositioned at any time.
The cone is fitted with a high-capacity fan directly connected to an internal airflow motor with Premium IE3 energy efficiency suitable for high-temperature operation (insulation class H). The cone is capable of continuous 360° rotation and has two rectangular tilting air outlets that distribute air uniformly over the cars and the surrounding pieces.
The installed power is just 2.2 kW, much lower for the same volume of moved air than a normal axial or centrifugal fan positioned above the dryers, which consumes on average between 5.5 and 7.5 kW. The low power consumption is a result of the cone’s aerodynamic design and the direct air path free from external ducting and the consequent bends and cross-sectional changes that typically cause power losses.
The speed of the air coming out of the slits is normally regulated by a frequency inverter, which guarantees more delicate ventilation in the first part of the cycle.
The cones rest on a self-supporting structure and are placed on the ground. All that is needed is to connect them to an electrical power cable and they are ready to use. The system allows for maximum flexibility. Units can be added, cones can easily be moved around inside the dryer for different car positioning (they have provision for handling with pallet trucks), they can be inserted into already installed dryers requiring better ventilation, or they can replace existing high-consumption ventilation systems (revamping).
Another important advantage concerns maintenance. The cones can be removed from the cell and all parts are readily accessible, ensuring ease of maintenance. They also simplify the configuration of the dryer as only the heat generation and moist air management equipment is positioned on the roof without the inconvenience of ducting, insulation and various access points.
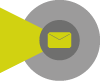
Did you find this article useful?
Join the CWW community to receive the most important news from the global ceramic industry every two weeks