Rapid Dry: the next-generation dryer
Setec is presenting its new low energy consumption dryer for sanitaryware and tableware. In operation since early 2022, it has exceeded its targets with a drying cycle of under 8 hours, heat consumption of 98 kcal/kg and electricity consumption of 0.003 kWh/kg.
Antonio Fortuna, Domenico Massimo Fortuna, Setec (Civita Castellana, Italy)

The recent dramatic increases in natural gas prices have made it more urgent than ever to drastically reduce the energy consumption of thermal machines in ceramic manufacturing processes. The Setec Group has long been one of the leading innovators in the industry and in recent years has focused on a number of energy-saving solutions. Thanks to European co-funding through the Life programme, it has developed new formulations for sanitaryware with a low firing temperature (Life Sanitser project) and a new generation of low energy consumption shuttle and tunnel kilns (Life Economick project).
The latest Life project involving Setec from June 2020 is Life Rapid Dry, which focuses on energy saving in the sanitaryware and tableware drying process. The project has two goals: construction of a low energy consumption dryer (described in this article) and optimisation of sanitaryware bodies by introducing recycled materials (the subject of a future article).
The Life Rapid Dry project saw the cooperation of LCE, an Italian company specialized in LCA, environmental and socio-economic impact assessment.
The drying process
Drying is an extremely important production stage that involves removing all non-chemically-bonded water from the body. This water may be present either in the spaces between the body particles (interstitial water) or on the surfaces around the particles.
In the drying process, water evaporates and air is used both as the heating fluid and as the means of evacuation of the vapour. So to regulate the drying process, it is essential to control the three air flow characteristics of temperature, relative humidity and speed.
To gain a better understanding of the phenomena associated with drying, we shall take a detailed look at the process mechanism and the conditions that control it.
When the article is removed from the casting mould, the particles that make up the body are surrounded by a capillary network of water. In order to evaporate, this water must migrate to the surface of the article during the drying process without damaging the integrity of the semi-finished product.
The two fundamental factors controlling drying are therefore the speed of diffusion of water through the thickness of the piece and the rate of evaporation. The conditions for optimal drying are achieved when the rate of evaporation is equal to or slightly lower than the rate of diffusion. This ensures that the water evaporates from the surface and prevents evaporation phenomena from occurring within the thickness of the body. As we shall see, these conditions rarely occur in industrial processes.
The rate of diffusion of water in capillary channels depends on two factors:
- the temperature of the piece (the rate of diffusion increases with temperature);
- the composition of the body: the higher the content of plastic and very fine materials in the body, the slower the rate of diffusion; a more plastic body will also be subject to greater shrinkage and therefore increased blockage of the channels through which the water flows, thereby reducing the rate of diffusion.
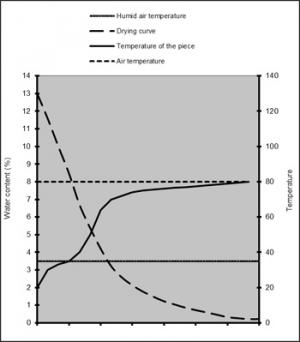
The water evaporation rate increases in three cases:
- when the difference between the vapour pressure inside the piece and the vapour pressure in the drying air increases (i.e. with increasing temperature);
- as the speed of the drying air increases;
- when the surface/volume ratio (i.e. the specific surface area of the article) increases.
Figure 1 shows the drying curve obtained when performing tests on a sanitaryware body at constant air temperature and humidity. Observing this curve, we can easily identify three separate phases.
Constant drying speed phase
In this phase, the rate of migration of water to the surface is greater than the rate of evaporation, resulting in the formation of a thin film of water over the entire surface of the piece. The water that is eliminated is the interstitial water that is capable of flowing relatively easily to the surface of the piece, causing it to shrink. This phenomenon is illustrated in Figure 2, which shows how the dimensions of a specimen change as a function of its water content (Bigot curve).
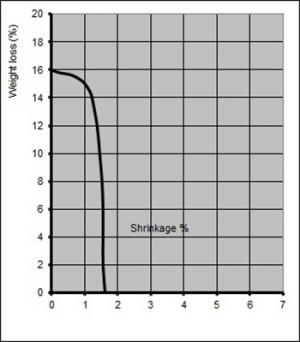
Decreasing speed phase
As the particles come closer together, the gaps through which water can pass are greatly reduced and the surface of the piece is no longer uniformly covered with water. Evaporation begins to take place within the thickness of the ceramic body, resulting in the migration of vapour to the surface. As the evaporation zone moves further towards the inside of the body, the drying speed decreases. The heat transferred to the surface of the piece no longer serves to evaporate the water and instead raises its temperature to values close to the dry bulb temperature. During this time, shrinkage continues until the particles come into contact with each other, at which point the shrinkage of the piece ceases and porosity begins to form.
Phase during which the speed decreases and tends towards zero
This section of the drying curve tends asymptotically towards zero, corresponding to the process of elimination of both the residual interstitial water and the superficial film of water around the solid particles. Water evaporation now occurs exclusively inside the piece. In this case, care must be taken to avoid sharp increases in the internal pressure of the water vapour as the piece is liable to suffer violent breakage if the pressure exceeds the material’s mechanical strength. This for example is what happens when pieces explode after being introduced into the kiln while they are still too moist.
From these considerations, it is easy to appreciate that no matter how carefully the conditions and distribution of hot air are controlled, even the best drying treatment cannot ensure the uniform drying of a sanitaryware article. This is particularly true for items such as washbasins, bidets and WCs, which have large surface sections sheltered from the hot air flow.
Uneven drying results in different degrees of shrinkage between one section of the surface and another, causing stresses in the ceramic body. When these stresses exceed the mechanical strength of the body, cracks or fissures are formed.
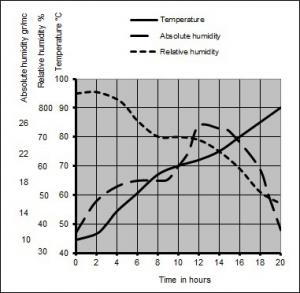
Drying must therefore be performed in such a way that the inevitable moisture gradients remain within acceptable limits. However, with traditional forced convection drying, this equates with longer cycle times. The pieces must therefore be heated with very humid warm air in order to even out the temperature throughout the ceramic body before the evaporation process begins. The relative humidity of the air is then gradually reduced in order to initiate evaporation, resulting in drying curves such as the one shown in Figure 3.
Traditional dryers vs. Rapid Dry
The purpose of dryers is to reduce the water content of the piece to final values of less than 1% by weight. Older machines do not have real control systems, but can be thought of as simple heated chambers capable at best of maintaining a constant temperature without humidity control. For this reason, drying cycles often have a duration of more than 14 hours and do not allow the introduction of excessively moist pieces.
In addition, temperature uniformity within the chamber is only achieved by introducing large volumes of air, usually distributed through perforated grilles. This makes it necessary to significantly oversize both the intake fans and the heat generator, resulting in significant levels of electricity and natural gas consumption.
The new Rapid Dry dryer is designed to address all these critical issues and brings advantages in terms of lower consumption and shorter drying cycle times.
Drawing on its more than 30 years’ experience in the ceramic sector, Setec has optimised the dryer’s heat flows and significantly improved control of the various parameters using innovative management software. This brings the following benefits:
- the ability to turn the heat generator on/off so that it supplies only the minimum amount of heat required and only when needed;
- reduction in speed/switching off of all electric motors (cones and fans), which only operate when necessary;
- autonomous temperature and humidity control using water mist to control the initial steps in the cycle in particular;
- improved homogeneity of the chamber by using motorised cones to create adequate fluid turbulence inside the dryer;
- optimisation of heat flows into and out of the chamber dryer.
Installation of the new Rapid Dry: results
The Rapid Dry dryer was started up in early 2022 thanks to the cooperation of the Civita Castellana-based company F.A. Ceramica which tested the dryer in its factory. The results meet and significantly exceed the aims of the Life project:
- Drying cycle under 8 hours,
- Heat consumption of 98 kcal/kg compared to the 288 kcal/kg of older generation dryers,
- Electricity consumption of 0.003 kWh/kg compared to the benchmark figure of 0.019 kWh/kg.
Clearly, these very positive improvements are the combined result of the innovations that have been introduced together with a significant reduction in drying times compared to standard dryers. This results not only in significant cost savings, but also in a drastic reduction in CO2 emissions.
These advantages can be seen first-hand by observing the Rapid Dry dryer in operation (for info: [email protected])
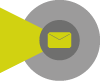
Did you find this article useful?
Join the CWW community to receive the most important news from the global ceramic industry every two weeks