Rapid Dry: l’essiccatoio di nuova generazione
Setec presenta il nuovo essiccatoio a basso consumo per sanitari e stoviglieria. Già in funzione da inizio 2022, presenta risultati superiori agli obiettivi, con un ciclo di essiccazione inferiore alle 8 ore, un consumo termico di 98 Kcal/kg e un consumo elettrico di 0.003 Kwh/kg.
Antonio Fortuna, Domenico Massimo Fortuna, Setec (Civita Castellana, Italy)

I recenti e incontrollati aumenti del prezzo del metano hanno reso ancor più urgente il bisogno di ridurre drasticamente i consumi delle macchine termiche nei processi di produzione di manufatti in ceramica. Il gruppo Setec, da sempre all’avanguardia dell’innovazione nel settore, negli ultimi anni ha focalizzato l’attenzione su diverse soluzioni volte al risparmio energetico; in particolare, grazie al cofinanziamento europeo del programma Life, sono state sviluppate sia nuove formulazioni per sanitari basso-cuocenti (Progetto Life Sanitser) che una nuova generazione di forni intermittenti e tunnel a basso consumo (progetto Life Economick).
L’ultimo progetto Life che ha coinvolto Setec a partire da giugno 2020 è il Life Rapid Dry, dedicato al risparmio energetico nel processo di essiccazione di sanitari e stoviglieria. Due gli obiettivi del progetto: la realizzazione di un essiccatoio a basso consumo (descritto in questo articolo) e l’ottimizzazione degli impasti per sanitari mediante l’introduzione di materiali di recupero (oggetto di un prossimo approfondimento).
Alla R&S di Life Rapid Dry ha collaborato anche la LCE, azienda specializzata nella valutazione degli impatti ambientali, socio-economici ed in LCA.
Il processo di essiccazione
L'essiccamento è una fase produttiva estremamente importante che provvede ad eliminare dall'impasto l'acqua non legata chimicamente; questa può essere o acqua interstiziale contenuta nei vuoti fra le particelle che costituiscono l'impasto, oppure acqua disposta superficialmente attorno alle varie particelle.
Nell'essiccamento l'acqua viene evaporata e, come fluido riscaldante, si usa aria che funge anche da mezzo di evacuazione del vapore. Per regolare il processo d'essiccazione è quindi fondamentale controllare le tre caratteristiche dell'aria, ossia: temperatura, umidità relativa e velocità.
Per comprendere meglio i fenomeni connessi all'essiccamento analizziamo in dettaglio il suo meccanismo e i suoi elementi controllanti.
Le particelle che costituiscono l'impasto, appena estratto dallo stampo di colaggio, si trovano circondate da un reticolo capillare d'acqua che, durante l'essiccamento, dovrà migrare alla superficie del pezzo per poter evaporare, senza danneggiare l'integrità del semilavorato.
I due fattori fondamentali che controllano l'essiccamento sono pertanto la velocità di diffusione dell'acqua attraverso lo spessore del pezzo e la velocità di evaporazione. Le condizioni per un essiccamento ottimale si hanno con la velocità d'evaporazione uguale o leggermente inferiore alla velocità di diffusione: si ha così un'evaporazione superficiale e si evita l'insorgere di fenomeni evaporativi all'interno dello spessore dell'impasto. Come vedremo, tali condizioni sono rispettate raramente nei processi industriali.
La velocità di diffusione dell'acqua nei canali capillari dipende da due fattori:
- la temperatura del pezzo (la velocità di diffusione cresce all’aumentare della temperatura);
- la composizione dell'impasto: più l’impasto è ricco di materiali plastici e molto fini, più la diffusione è lenta; un impasto più plastico sarà anche soggetto ad un maggior ritiro e quindi ad una maggiore occlusione dei canali di passaggio dell'acqua con la conseguente riduzione della sua velocità di diffusione.
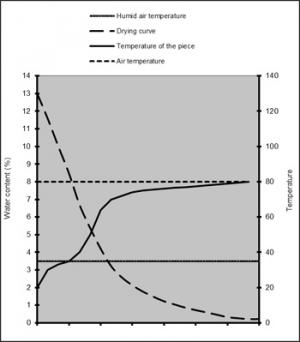
La velocità di evaporazione dell'acqua cresce in tre casi:
- quando aumenta la differenza fra la sua tensione di vapore nel pezzo e la pressione di vapore nell'aria d'essiccamento (quindi con la sua temperatura);
- quando aumenta la velocità dell'aria d'essiccamento;
- quando aumenta il rapporto superficie/volume, ossia la superficie specifica del manufatto.
La Figura 1 mostra la curva d'essiccamento ottenuta effettuando delle prove su un impasto di sanitario, mantenendo costanti la temperatura e l'umidità dell'aria. Analizzando tale curva si individuano facilmente tre fasi distinte.
Fase a velocità d'essiccamento costante
In questa fase la velocità di migrazione dell'acqua alla superficie è superiore a quella d'evaporazione; si ha quindi un sottile strato d'acqua su tutta la superficie del pezzo. L'acqua eliminata è quella interstiziale che affluisce con relativa facilità alla superficie del pezzo causando il ritiro dello stesso; questo fenomeno è evidenziato nella Figura 2 che riporta la variazione dimensionale di un provino in funzione del suo contenuto d'acqua (curva di Bigot).
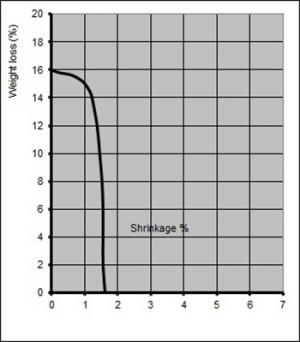
Fase a velocità decrescente
L'avvicinamento delle particelle provoca una notevole riduzione delle aperture disponibili per il passaggio dell'acqua e quindi la superficie del pezzo non è più uniformemente ricoperta di liquido. Inizia il fenomeno dell'evaporazione all'interno dello spessore della massa ceramica, con la conseguente migrazione del vapore alla superficie. Più la zona di evaporazione si sposta verso l'interno, minore è la velocità d'essiccazione. Il calore ceduto alla superficie del pezzo, non più utilizzato per l'evaporazione dell'acqua, ne innalza la temperatura fino a valori prossimi a quelli del bulbo asciutto. Durante questo periodo il ritiro continua fino a quando le particelle vengono in contatto fra loro; a questo punto cessa la contrazione del pezzo ed inizia la formazione di porosità.
Fase a velocità decrescente, tendente verso lo zero
Questo tratto della curva d'essiccamento tende asintoticamente allo zero e corrisponde all'eliminazione dell’acqua interstiziale residua e dell'acqua disposta come una pellicola sulla superficie delle particelle solide. L'evaporazione dell'acqua avviene esclusivamente all'interno del pezzo; in questo caso si deve avere l'accortezza di non provocare bruschi innalzamenti della pressione interna del vapore d'acqua perché, se questa supera la resistenza meccanica del materiale, si può avere la rottura violenta del pezzo: è il caso delle "esplosioni" che avvengono quando si introducono pezzi ancora troppo umidi nel forno di cottura.
Da quanto esposto si deduce facilmente che, per quanto le condizioni e la distribuzione dell'aria calda siano controllate, anche il miglior trattamento d'essiccamento non può assicurare l'essiccazione omogenea di un sanitario. Questo è ancora più vero per pezzi come i lavabi, i bidet o i vasi, che presentano grandi porzioni della loro superficie "in ombra" rispetto al flusso dell'aria calda.
Un essiccamento disomogeneo si traduce in ritiri differenti da una zona all'altra della superficie di un pezzo che inducono delle tensioni nella massa ceramica; quando tali sforzi superano in valore la resistenza meccanica dell'impasto si ha la formazione di crepe o fessure.
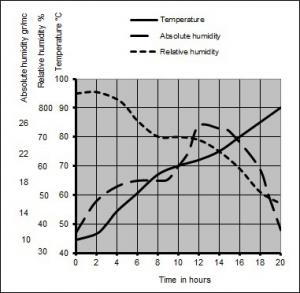
È quindi necessario condurre l'essiccamento in modo che i gradienti di umidità, inevitabili, si mantengano dentro limiti accettabili. Tuttavia, con l'essiccamento tradizionale a convezione forzata, questo significa allungare i tempi di ciclo. Infatti, è necessario operare un riscaldamento dei pezzi con aria calda ma molto umida, così da uniformare la temperatura in tutta la massa ceramica prima che inizi il processo evaporativo; si riduce quindi gradatamente l'umidità relativa dell'aria per attivare l'evaporazione, ottenendo curve d'essiccamento come quella riportata in Figura 3.
Essiccatoi tradizionali vs. Rapid Dry
Gli essiccatoi, come noto, servono per ridurre il contenuto d’acqua del pezzo a valori finali inferiori dell’1% in peso. Le macchine di più vecchia concezione non hanno veri e propri sistemi di regolazione, ma sono assimilabili a delle “camere riscaldate” in cui, al massimo, si cerca di mantenere una temperatura costante rinunciando al controllo dell’umidità. Per questo motivo i cicli di essiccamento si attestano molto spesso sopra le 14 ore e non permettono l’introduzione di pezzi troppo umidi.
In aggiunta, l’uniformità di temperatura all’interno della camera è ottenuta solo grazie all’immissione di grandi quantità di aria, distribuita solitamente mediante opportune griglie forate. Tutto questo costringe ad un notevole sovradimensionamento sia dei ventilatori di mandata che del generatore di calore con notevole dispendio di energia elettrica e metano.
L’obiettivo del nuovo essiccatoio Rapid Dry è intervenire su tutte le criticità descritte, apportando benefici sia in termini di consumi che di riduzione della durata del ciclo di essiccamento.
Forte dell’esperienza ultra-trentennale nel settore ceramico, Setec ha ottimizzato i flussi di calore dell’essiccatoio e ha migliorato sensibilmente il controllo dei vari parametri grazie ad un innovativo software di gestione che consente:
- l’accensione/spegnimento del generatore di calore, che eroga quindi il minimo calore necessario solo quando serve;
- la riduzione dei giri/spegnimento di tutti i motori elettrici (coni e ventilatori) che funzionano solo quando necessario;
- la gestione autonoma di temperatura e dell’umidità con l’impiego di acqua nebulizzata per controllare in particolare gli step iniziali del ciclo;
- una migliore omogeneità della camera mediante l’utilizzo di coni motorizzati in grado di creare un’adeguata turbolenza fluidodinamica all’interno dell’essiccatoio;
- l’ottimizzazione dei flussi di calore in ingresso ed uscita dall’essiccatoio a camera.
Installazione del nuovo Rapid Dry: risultati ottenuti
L’essiccatoio Rapid Dry è stato avviato ad inizio 2022 grazie anche alla collaborazione della F.A. Ceramica di Civita Castellana che ha testato l’essiccatoio nel suo stabilimento. I risultati ottenuti non solo rispettano gli obiettivi indicati nel progetto Life, ma li migliorano sensibilmente:
-
Ciclo di essiccazione inferiore alle 8 ore,
- Consumo termico di 98 Kcal/kg contro le 288 Kcal/kg degli essiccatoi di vecchia generazione,
- Consumo elettrico di 0.003 Kwh/kg invece di 0.019 Kwh/kg rispetto al riferimento.
È evidente che tali miglioramenti, eccezionalmente positivi, sono dovuti alla combinazione delle innovazioni introdotte, unite ad una sensibile riduzione dei tempi di essiccazione rispetto agli essiccatoi standard. Tutto questo si traduce non solo in un notevole risparmio economico, ma anche in una drastica riduzione delle emissioni di CO2. Vantaggi che si possono verificare direttamente visitando l’essiccatoio Rapid Dry in funzione (per info: [email protected])
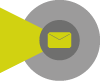
Hai trovato utile questo articolo?
Unisciti alla community di CWW per ricevere ogni 15 giorni le principali novità da tutto il mondo sul settore ceramico